Background
Soft sensors, also known as inferentials, play a crucial role in industrial processes by predicting important lab values or other slow-sampled variables. In many manufacturing environments, the process involves monitoring various parameters that are critical for quality control or process optimization. However, some of these parameters, such as lab values, are slow to sample due to the time required for testing. This delay can hinder real-time decision-making and potentially lead to inefficiencies or quality issues. Soft sensors offer a solution to this challenge by using fast-sampled inputs as inputs to a machine learning model. This model can then predict the slow-sampled variables, providing real-time insights without the need to wait for hours for the next lab sample to be tested. Operators can monitor these predictions and make timely adjustments to the process, optimizing operations and ensuring quality standards are met.
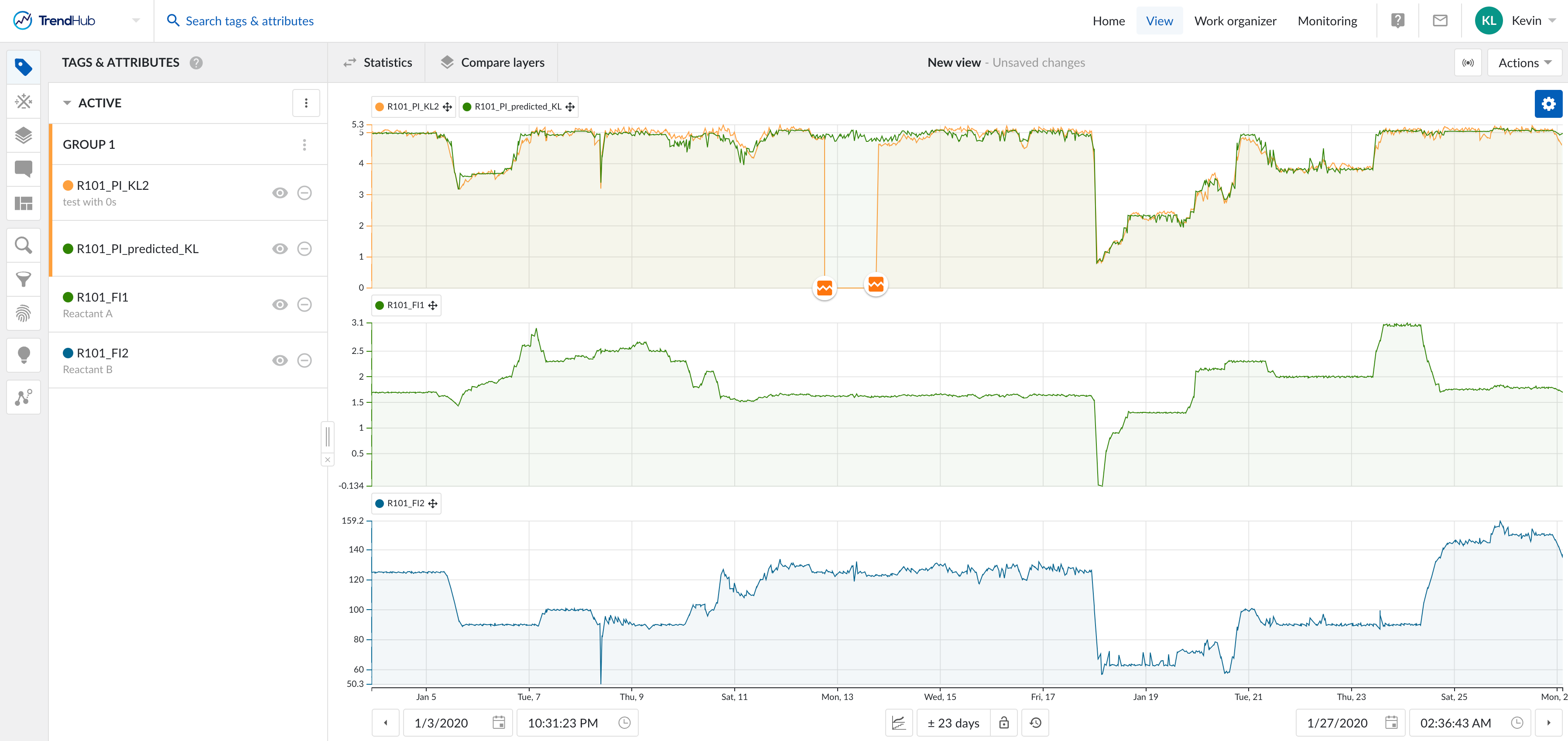
Challenge
Our primary challenge is to develop a machine learning model that can accurately predict and mimic a true label tag, specifically a slow-sampled tag such as a lab value. The goal is to create an output tag that closely tracks all future lab values, ensuring that increases in the output tag correspond to increases in the lab results. To achieve this, we need to carefully select the inputs to the machine learning model, ensuring that they are relevant to the prediction task.
One of the key considerations is the independence of the input tags. We need to ensure that the inputs are independent of each other to avoid issues of collinearity, where two or more inputs are highly correlated. Collinearity can lead to instability in the model and make it difficult to interpret the importance of individual features.
Another challenge is the selection of an appropriate machine learning model and the tuning of hyperparameters. We plan to experiment with different models, such as linear regression, decision trees, and neural networks, to find the best-performing model for our use case. Additionally, we will tune the hyperparameters of the selected model to optimize its performance and ensure that it can accurately predict the future lab values.
Overall, the challenge lies in developing a machine learning model that can effectively predict and mimic the slow-sampled lab values, ensuring that the output tag closely tracks the true lab values and provides valuable insights for process optimization and quality control.
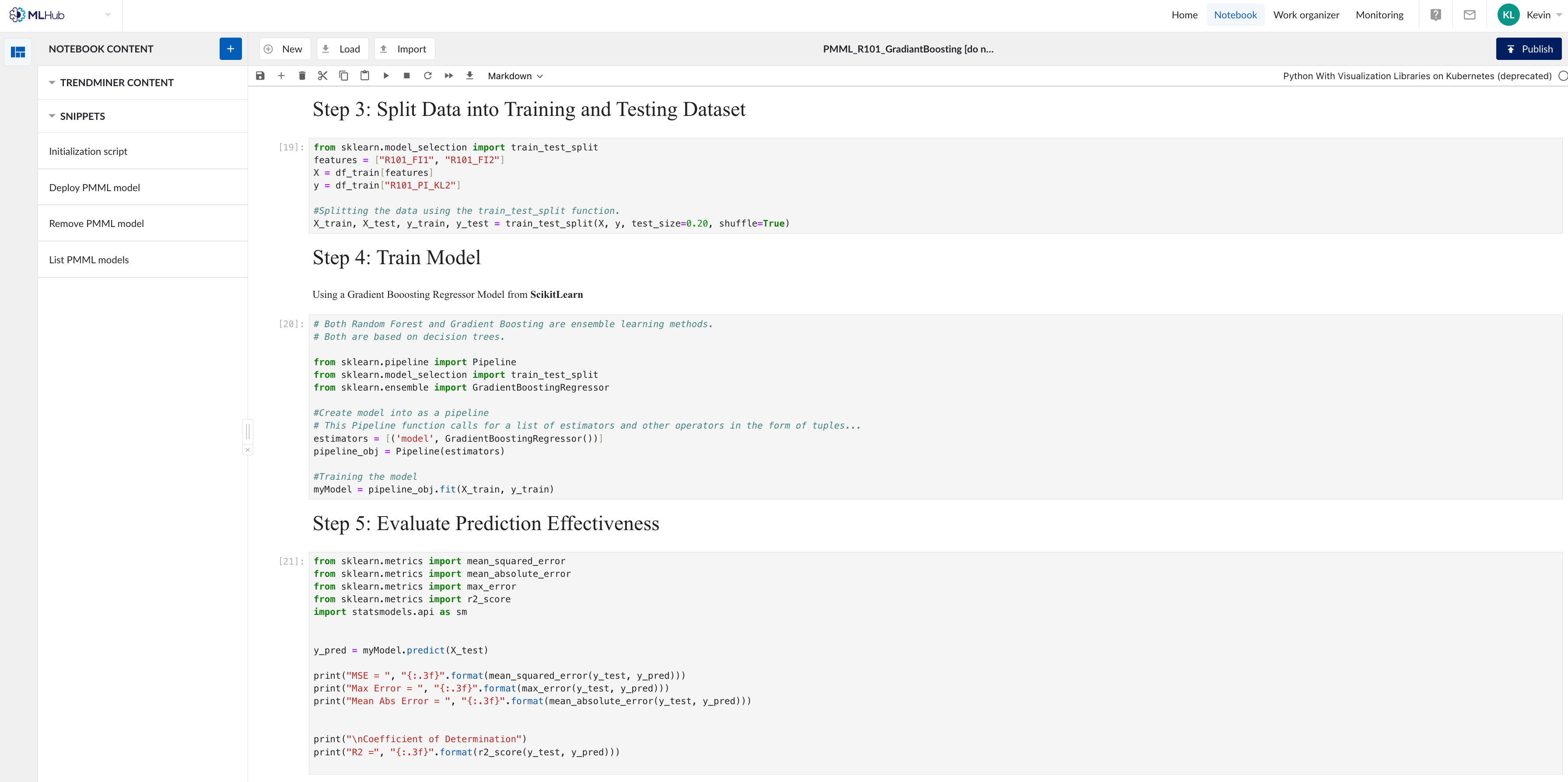
Solution
To address the challenge of predicting slow-sampled variables in real-time, we implement a soft sensor solution using TrendMiner's functionalities. The first step involves identifying the fast-sampled inputs that can serve as predictors for the slow-sampled variable, such as a lab value. These inputs are selected based on their correlation and relevance to the target variables.
Next, we use TrendMiner's machine learning capabilities in MLHub to train a predictive model using the selected inputs. The model is trained to accurately predict the slow-sampled variables based on the fast-sampled inputs, taking into account the process dynamics and interdependencies between variables.
Once the model is trained and validated, it is deployed in TrendHub, where it continuously updates based on the fast-sampled inputs and provides real-time predictions for the slow-sampled variable. Operators are able to access these predictions through a user-friendly interface, allowing them to monitor the process and make adjustments as needed to optimize operations and ensure quality standards are met.
By implementing this soft sensor solution, we are able to overcome the limitations of traditional sampling methods and improve our ability to predict and control critical process parameters in real-time.
Value
The implementation of the soft sensor solution using TrendMiner's functionalities can result in significant value for operations teams. Firstly, the real-time prediction of slow-sampled variables, such as lab values, can enable operations and engineering to make proactive decisions and adjustments to the process, leading to improved efficiency and quality. By eliminating the need to wait for lab samples to be tested, operations can experience reduced delays and downtimes, resulting in increased productivity.
Furthermore, the predictive insights provided by the soft sensor can optimize processes and reduce waste. Operators can quickly identify and address potential issues before they escalate, leading to cost savings and improved overall performance. Additionally, the user-friendly interface of the soft sensor solution makes it easy for operators to access and interpret the predictions, empowering them to take informed actions in real-time.
Overall, the implementation of the soft sensor solution has the ability to enhance operational efficiency, improve product quality, and reduce costs, demonstrating the value of leveraging advanced analytics in industrial processes.