Background
This use case is centered on a mixing tank, where the streams of two distinct products are joined. The intermediate products are continuously added to the mixing tank until it reaches a certain level. At that point, a sample is taken for analysis, and the tank is emptied into a larger storage tank.
Challenge
Over the span of a few weeks, there have been crystallization issues with one of the two products. This undesired crystallization interferes with sensors leading to unreliable measurements, which can lead to quality issues as the mixture is processed further.
We needed to find the root cause of these crystallization issues.
Solution
- Visualizing the problem
The composition of the samples from the mixing tank was displayed in TrendMiner. Here we could clearly see the concentration of the solvent product decreasing, which is an obvious cause of the other product crystallizing. The question thus becomes: why are we receiving less solvent from our production process?
- Hypothesis generation
Since there were no obvious hypotheses to check, we resorted to the Cross-Correlations functionality in TrendMiner, which allows for searching all tags in TrendMiner for correlations. Using this functionality on the slowly decreasing trend of solvent concentration yielded a significant correlation with the drop in level in a tank elsewhere in our process.
- Hypothesis investigation
Zooming out in TrendMiner, we noticed that the level in this particular tank first sharply increased and then slowly decreased. This matches the addition of an external intermediate product to the process, which is then mixed into internally produced product in this tank. As this external product is processed and the level in the tank drops to normal levels, the solvent concentration downstream in our process decreases. This points to the addition of external intermediate product as a cause for the process issues. Looking at historic data when external intermediate product was added, the same issues occurred there, confirming this hypothesis.
- Uncovering the failure mechanism
Further investigation in TrendMiner revealed the mechanism by which the external intermediate product influenced the solvent stream: a higher recycle flow was implemented upstream in the process to deal with the different product composition. This increased recycle also impacted other properties, however, which eventually led to a different split ration of solvent and other components. As less solvent eventually reaches our mixing tank, crystallization issues start to occur.
Value
A clear root cause and its mechanism have been uncovered using TrendMiner. Many of the steps required to come to a full understanding of this issue would not have been possible in other tools.
Now that the cause of the issues is known, corrective action can be taken whenever external intermediate product is added to the process.
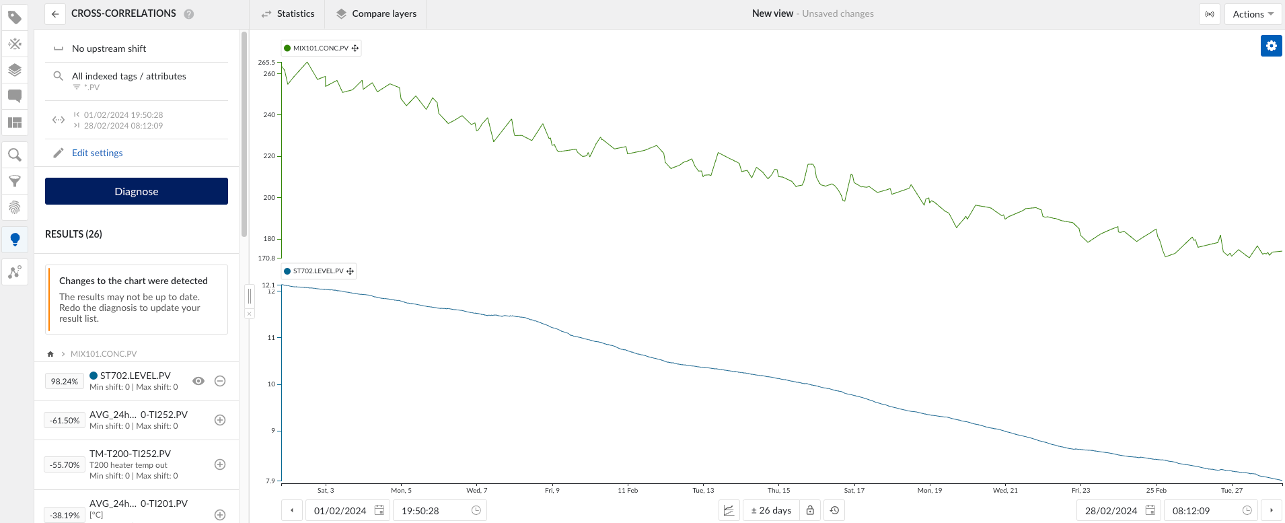