Background
In our batch process, ensuring optimal operating conditions is critical for maintaining production, product quality and worker safety. Monitoring various process parameters such as low average temperature, constant pressure, high end- concentration and low energy consumption in real-time is essential to maintain consistency and quality across batches.
Challenge
Our challenge was to implement a comprehensive system for monitoring operating conditions in a batch process with 7 regularly changing recipes. Over the past month, we have experienced problems with parameters deviating from optimal process conditions, resulting in poor product quality. We needed a solution that would accurately monitor the trend profiles at each step of the process and alert operators when these deviations occurred. The alert should provide actionable insight for operators and supervisors to optimize production processes and minimize product loss.
Solution
1. Visualizing the trends
A list of tags was added to a TrendHub view, including the temperature, pressure, concentration, energy consumption, end-product quality from the laboratory and the information about the product type. It was super fast and allowed us to see the last two campaigns, which we then used for analysis.
2. Identify batches with optimal process conditions
The value-based search was the perfect functionality to search for similar product types, returning a list of all events of one product type in the past.
From there we added the following calculations to the search results:
- Total energy consumption (Integral)
- Maximum concentration
- Average Pressure
- Average Temperature
- End value of End-product quality
The event analytic functionalities allowed us to see all aggregated values in histogram and parallel coordinate plots from where we could easily refine the results and visualize 15 optimal batches as a representative sample.
3. Golden Batch Fingerprint
Utilizing the fingerprint functionality, we capture the minimum and maximum values of active tags and create a hull curve that represents the optimal process conditions.
4. Fingerprint Monitoring
In the final step, we activated a fingerprint monitor that sends email alerts to the team. Whenever the alert is triggered, the recipient can click the link in the email, directly see which parameter went off and initiate a feedback cycle to correct the deviations.
Value
TrendMiner's real-time monitoring capabilities allowed us to maintain product quality standards by detecting deviations and ensuring consistent performance. As a result, we were able to optimize our production process and maximize throughput. The optimized operations led to significant cost savings by reducing downtime, minimizing energy consumption, and reducing product loss.
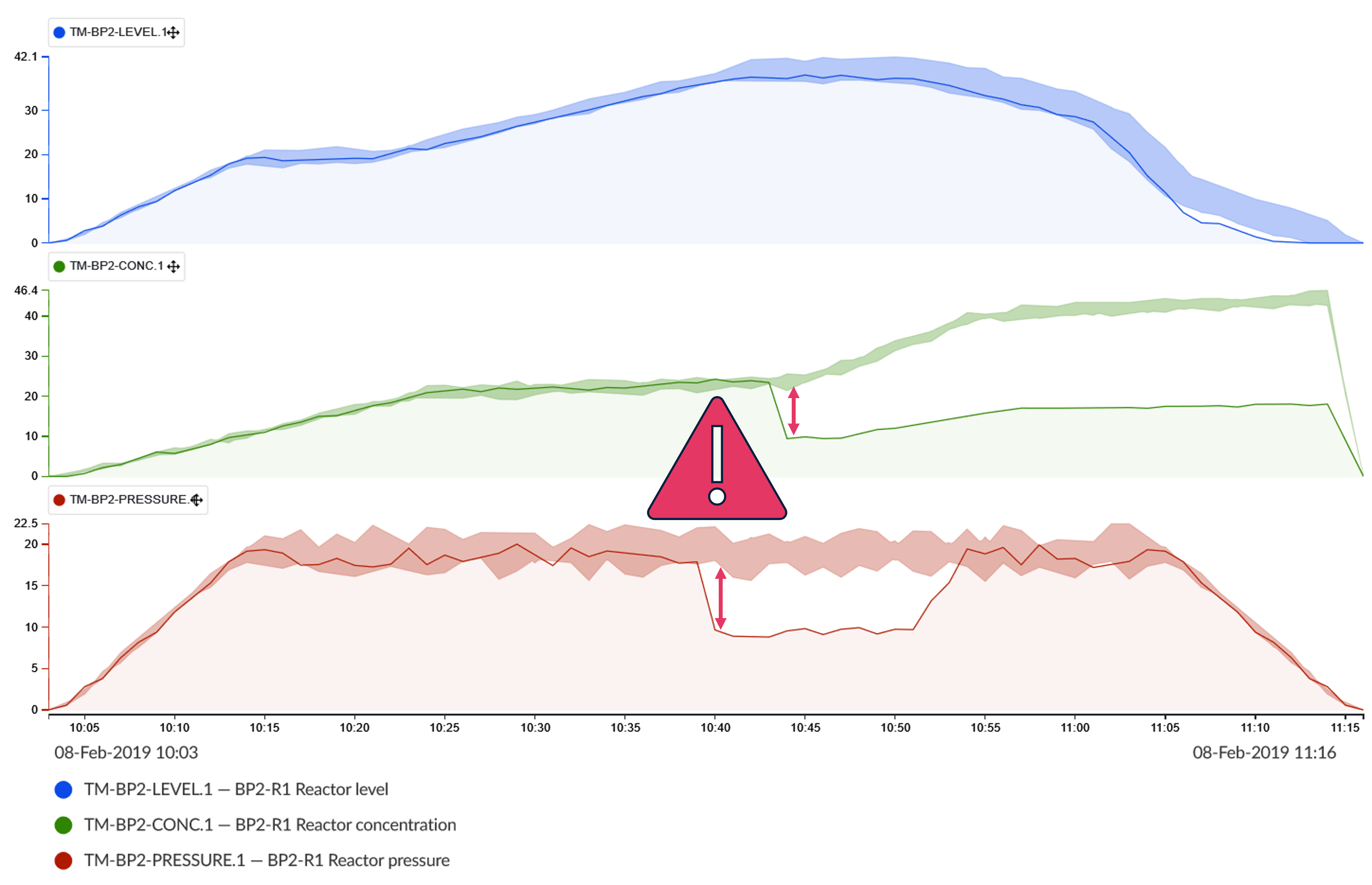