For rotating equipment, we need to seal off moving components with mechanical seals that use a barrier fluid. There is no way to seal off moving components perfectly so there will always be some leakage. If product leakage to the environment is unacceptable (typically for SHE reasons), a zero emission seal needs to be used. For zero emission seals, there can only be leakage from the barrier fluid into the product, which is why a barrier fluid that is under higher pressure than the pumped fluid needs to be used that is compatible with the product. After all, at least some of this barrier fluid will end up in the product. A classical example of this is the usage of N2 as a barrier fluid to natural gas.
Mechanical seals are common but critical components, and they can be monitored quite easily in TrendMiner as the monitoring criteria are simply value-based. We can sometimes use a value-based search directly, but if we need to compare two measurement (e.g. to ensure a difference in pressure is sufficient), we need to make a formula tag first.
All-in-all, the steps to follow up mechanical seals in TrendMiner are typically the following:
- Create a formula tag giving the difference between the barrier fluid (e.g., N2) and the pumped fluid (e.g., natural gas). This value should be above a (positive) threshold at all times.
- Search for when our pressure difference is below our allowed threshold. To avoid our eventual monitoring from triggering when our equipment is not running, we can include the criterion in our search that our operating pressure is significant.
- Set up a monitor on our search that notifies us when the search triggers.
- Create a dashboard with an overview of the status of your seals. Potentially you can include a log of historic events as well (context items coming from the monitor).
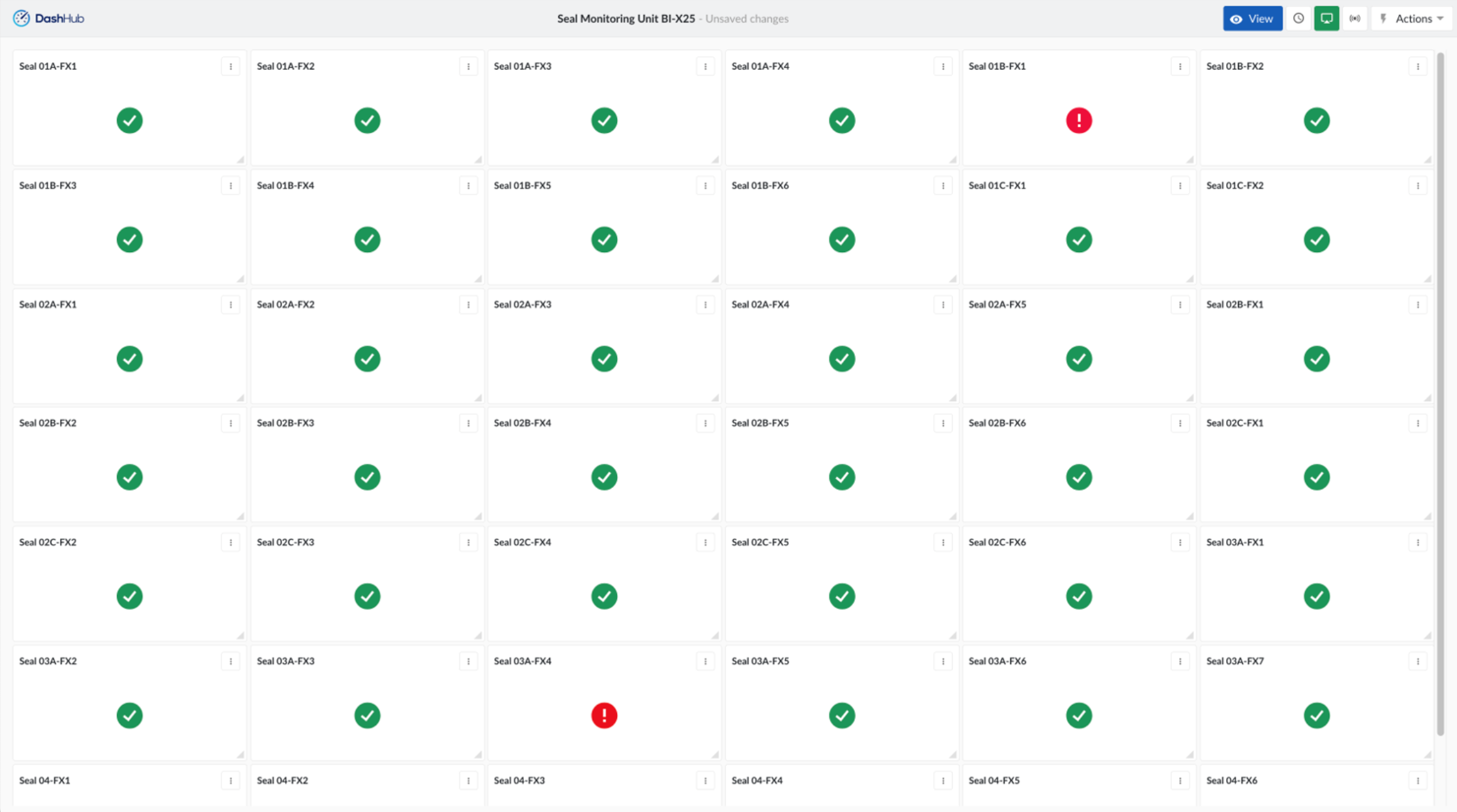
Besides differential pressure, many other parameters could be monitored, all following a similar workflow as the one detailed above. Typical other monitoring targets include:
-
Barrier fluid level. Can be monitored as an absolute value, or by the speed it decreases by first creating a flow rate tag.
-
Barrier fluid temperature. Especially useful when barrier fluid temperature control is dependent on a seal cooler.
-
Other barrier fluid properties such as pressure and flow rate.
-
Pumped fluid properties such as pressure, flow rate and temperature